FINAL ASSEMBLY LANE TECHNICAL SUPPORT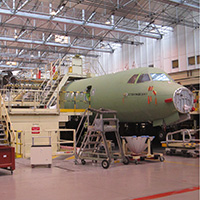
We propose to our customers the Representation and technical Follow up at Final Assembly Line (FAL) during manufacturing and delivery of the aircraft. This representation is performed through the provision of Expert(s) on-site the OEM facilities (AIRBUS & ATR) based in Toulouse. The objective is to ensure the on-time, on-cost and to specification completion of the manufacturing process up to the TAC (Technical Acceptance Completion). We perform an efficient and pro-active supervision of the OEM activities through the several technical services.
Our representative(s) will initiate a kick-off meeting at the beginning of each aircraft in order to obtain a tentative planning from the OEM in accordance with contractual delivery date and install a concession management agreement.
The inspections are conducted in accordance with the OEM Basic Customer Inspection Requirements and follow the sequence here under:
• Inspect during OEM presentations.
• Record deviations in the QLB (Quality Log Book) and make pictures of important issues.
• Re-inspect deviations after corrective actions.
• Review all concessions reported, recommend follow-up actions and follow up on close out actions.
PHYSICAL INSPECTION & ACTIVITIES:
- FAL Inspections support:
Our Representative(s) perform inspections when required by the OEM at the zone presentation in accordance with Customer Inspection Manual Chapters 2, 3 and 4:
- Paint Inspection Support:
Our Representative(s) perform paint inspection when required by the OEM:
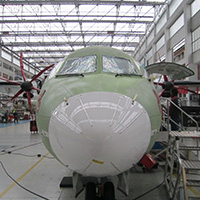
• Check the paint quality.
• Check the correct application of the livery in accordance with the approved paint drawings.
• Check the aerodynamic sealant and smoothness.
• Check windows and windshields condition.
- Cabin Inspection Support:
Our Representative(s) shall perform the cabin inspection when required by the OEM:
• Cabin installation.
• Cabin cosmetic parts inspection.
• Check the correct cabin installation as per the approved Cabin Layout.
• Check the Emergency Equipment's as per the Approved Emergency Equipment Layout.
If required by our customer, we can check the BFE (Buyer Furnished Equipment) to ensure the compliance with requirements, and correct condition/delivery.
- Acceptance phase Technical Support:
Our Representative(s) shall attend the following activities:
• Leak checks. (Strongly recommended).
• Ground Checks.
• Engine Runs.
• Acceptance flight.
These activities are performed in accordance with the OEM CAM (Customer Acceptance Manual).
RECORDS INSPECTIONS & ACTIVITIES:
- OEM Concessions review.
- LRU / LLP inventory and check as much as possible.
- Delivery Documents review.
- Delivery Documents compilation and scanning.
OTHERS ACTIVITIES:
Upon customer request, our Representative(s) can assist during the following activities:
- Technical Support during NAA (National Authority Agency) inspections.
- Attend the NAA aircraft inspection.
- Provide mandatory certificates and paperwork compilation. - Technical support during Commitment Letter negotiation and issuance.
- Ferry Flight coordination after ToT (Transfer of Title).
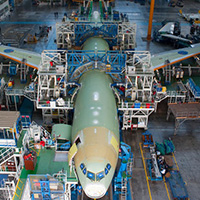
REPORTING & DELIVERABLES:
- During Final Assembly, a weekly report for each aircraft with dedicated pictures (if any) is sent by E-mail to the customer assigned persons. This report relates the aircraft assembly process progress, including the manufacturing deviations and the concessions management, it lists the discrepancies discovered during physical and records inspection.
- In case of important deviations or defects recorded during a Presentation, the customer assigned persons are immediately contacted by our Representative by phone and/or E-mail, in order to define the recovery actions.
- In order to ease the access to the documentation, we open an FTP session protected by password with access granted to the customer named representatives.
- At the TAC of each aircraft, if not available, a binder grouping all mandatory documents is built and delivered to our customer.